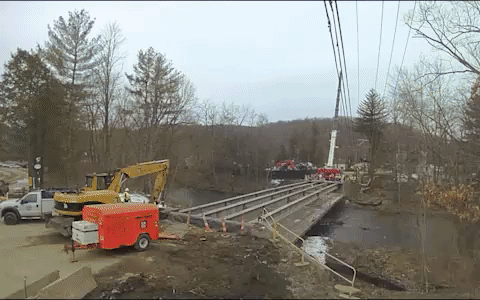
The Connecticut Department of Transportation’s (CTDOT’s) Bogue Road Bridge (CTDOT Bridge No. 05059) provides a critical connection within both the City of Torrington and Town of Harwinton transportation network. It links several major commercial businesses with convenient access to the state’s highway system. The bridge was originally constructed by O&G Industries of Torrington, Connecticut, in late 1956 after the historic flood of 1955 washed away the original bridge.
Approaching the end of its useful life, the bridge was recently deemed structurally deficient and required rehabilitation to avoid future traffic and safety impacts. Complicating rehabilitation, however, the bridge’s location posed construction challenges. With no viable long-term detour route available to accommodate the commercial traffic that relies on the bridge daily, in addition to a narrow bridge deck which precluded staged construction, the bridge could not be closed for the duration required for traditional rehabilitation. To overcome this, VHB’s design solution incorporated accelerated bridge construction (ABC) techniques and innovative technologies tailored to resolve the specific challenges facing the bridge’s construction that allowed it to be rehabilitated and reopened to traffic in just 22 days.
VHB’s bridge design included some first-ever methods and materials for the State of Connecticut. Among these was the use of AccelBridgeTM precast deck panels, a proprietary deck panel replacement system. The AccelBridgeTM deck system is a patented product fabricated exclusively by Fort Miller Precasters that features full-depth and full-width precast deck panels with a match-cast joint system. The system installation saves time and money by eliminating internal deck post-tensioning and transverse closure pours, and maintains deck compression through the use of an external deck jacking procedure. Simultaneously as an additional benefit, this procedure provides additional strength to the bridge which increases the structure’s original vehicle load-carrying capacity.
Other ABC technologies utilized by VHB included a partial thickness Ultra High Performance Concrete (UHPC) link slab, modeled after the New York State Department of Transportation (NYSDOT) UHPC link slab. Using this slab eliminated the need for deck joints and improved the bridge’s future resiliency.
“At VHB we are passionate about making meaningful contributions to the communities we serve,” said VHB Project Manager, Josh Colella, PE. “This project’s unique challenges provided our team the perfect opportunity to innovate creative solutions and deliver to the client and the community a bridge structure that will serve them well into the future.”
VHB has been involved in this project through its entire lifecycle, first performing the rehabilitation study, then leading rehabilitation design, and finally, offering bid and construction phase services. Additional services provided by the VHB team included light detection and ranging (LiDAR) survey scanning, a geotechnical subsurface program, environmental permitting, deck core sampling and materials testing, right-of-way (ROW) property map development, structural rehabilitation and roadway improvement design, plan production, and CTDOT Load Rating.
Learn more about VHB’s work with State DOTs through our transportation page, and to learn more about his project, connect with Josh via email or on LinkedIn.